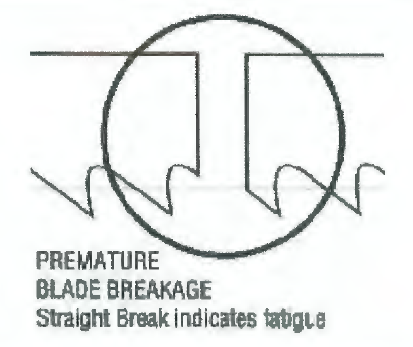
|
• Incorrect Blade • Band tension too high • Excessive feed • Incorrect cutting fluid • Wheel diameter too small for blade width • Worn or chipped pressure block • Blade rubbing on wheel flange • Teeth in contact with work before starting sawing • Side guides too tight |
• Check tooth selection • Reduce band tension, refer to operators manual • Reduce feed pressure • Check coolant recommendations • Use narrower blade • Replace worn pressure blocks • Adjust wheel alignment • Allow blade clearance above work • Refer to operators manual |
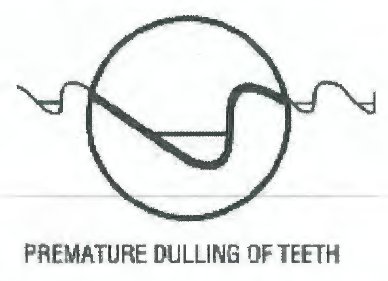
|
• Blade on machine backwards • Improper blade break-in procedure • Hard material or heavy surface scale • Material is work hardening • Improper cutting fluid or mix ratio • Speed or feed too high |
• Install blade correctly • Refer to recommended procedures • Check material hardness and surface condition • Increase feed pressure • Follow coolant mixing procedures • Check cutting recommendations |
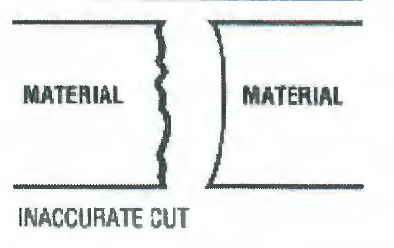
|
• Guide arms too far apart • Blade worn out • Over or under feeding • Improper tooth pitch • Curing fluid not applied properly • Too many teeth for material cross-section • Guides worn or loose |
• Adjust guide arms closer to material • Replace blade • Check cutting recommendations • Use proper tooth selection • Adjust coolant nozzles • Use proper tooth selection • Tighten or replace guides |
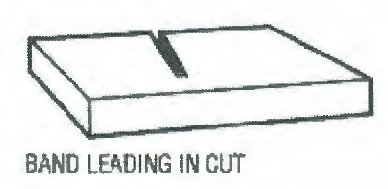
|
• Over feeding • Low band tension • Tooth set damaged • Guide arms loose or space too wide |
• Check cutting recommendations • Refer to operators manual • Check material hardness • Adjust guides and guide anns |
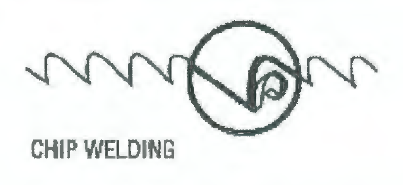
|
• Worn or missing chip brush • Improper or lack of cutting fluid • Wrong coolant ratio • Excessive feed or speed • Incorrect blade pitch |
• Replace or adjust chip brush • Check coolant flow and fluid type • Check coolant type and ratio • Reduce feed or speed • Use proper tooth selection |
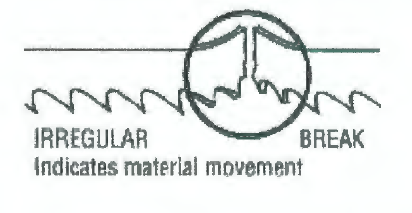
|
• Indexing while blade in work • Blade not high enough before index • Saw head drifts into work while neutral |
• Adjust index sequence • Adjust height selector • Check hydraulic cylinder |
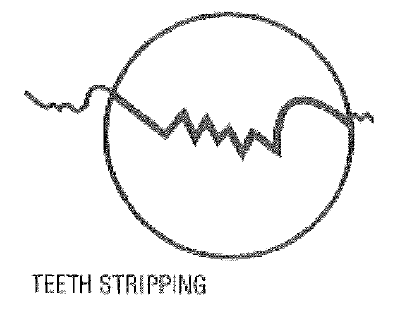
|
• Improper blade break-in procedure • Speed too slow • Feed pressure to high • Tooth jammed in cut • Poor cutting fluid application or ratio • Hard material or heavy scale • Wrong blade pitch • Work spinning or loose nested bundles • Blade on backwards |
• Follow proper break-in procedure • Refer to cutting recommendations • Reduce feed pressure • Do not enter new blade in that cut • Adjust coolant flow and ration • Check material or surface hardness • Use proper tooth selection • Tighten vises or use nesting clamps • Install blade correctly |
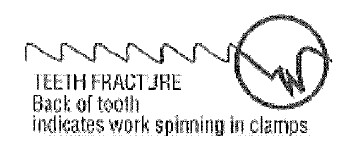
|
• Saw guides not properly adjusted • Incorrect feed or speed • lncorrect blade • Material moved in vise |
• Align or adjust saw guides • Refer to cutting recommendations • Use proper blade type and pitch • Inspect and adjust vises |
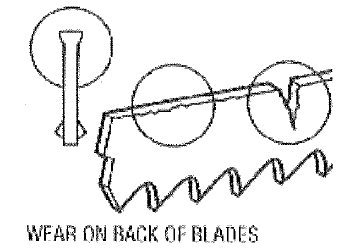
|
• Excessive back-up guide preload • Low blade tension • lncorrect blade (carbon steel type) • Excessive feed rate or pressure • Damaged or worn pressure block • Guide arms spaced too far apart • Blade rubbing band wheel flanges |
• Adjust pressure blocks • Refer to operators manual • Switch to a Bimetal blade • Reduce feed rate or pressure • Replace pressure block • Adjust guide arms closer to work • Adjust wheel alignment |
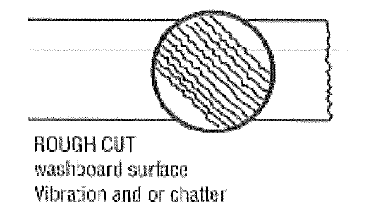
|
• Dull or damaged blade • lncorrect feed or speed • Blade not supported properly • Low blade tension • lncorrect tooth pitch • Guide arms too far apart |
• Install new blade • Refer to cutting recommendations • Adjust or tighten guide arms • Refer to operators manual • Use proper tooth selection • Adjust guide arms closer to material |

|
• Saw side guides too tight • Blade riding too high in guide • Blade teeth riding on band wheel surface • Wrong blade width for machine • Chips be carried back into cut • Worn or damaged pressure block • Insufficient coolant flow |
• Adjust guides properly • Adjust rollers or pressure blocks • Adjust tracking or replace wheel • Refer to operators manual • Replace or adjust chip brush • Replace pressure block • Adjust coolant flow |
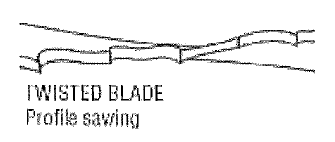
|
• Blade binding in cut • Side guides are too tight • Work loose in vise • Feed to heavy • Guide arms too far apart |
• Adjust feed or use heavy set blades • Adjust guides • Adjust vises • Reduce feed pressure • Adjust guide arms closer to material |
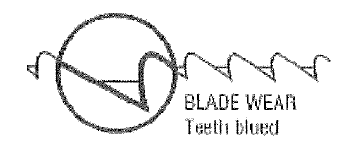
|
• Incorrect blade • Heavy feed or too fast speed Lack of cutting fluid • Blade installed backwards |
• Use proper tooth selection • Refer to cutting recommendations • Adjust coolant flow or ratio • Install blade correctly |
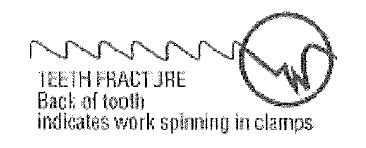
|
• Material loose in vise • Incorrect tooth pitch • Feed too fast • Speed too fast |
• Adjust vises • Use proper tooth selection • Reduce feed rate • Refer to cutting recommendations |